Mastering Construction Efficiency: A Guide to Connectivity and Fleet Management
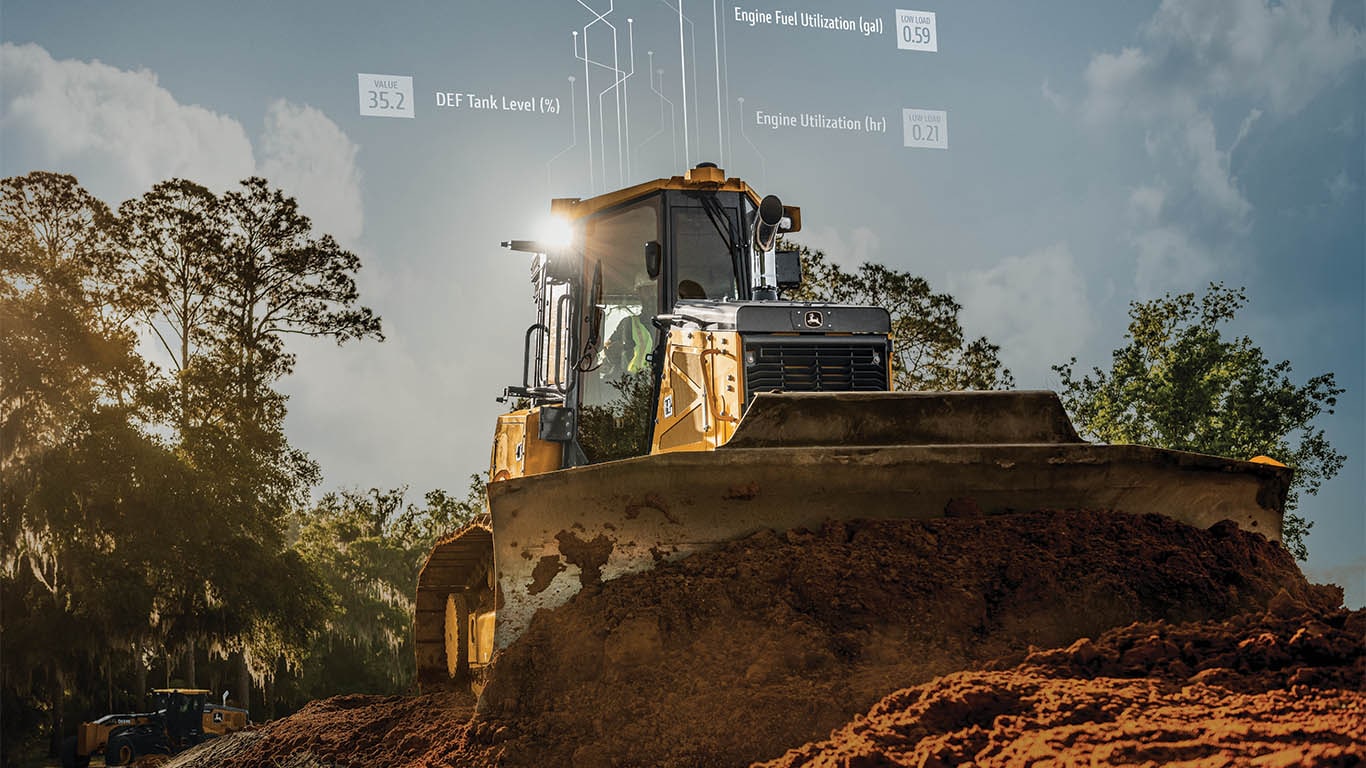
You can't be everywhere all at once. That's why John Deere offers connectivity and other fleet management solutions to help you with everything from machine monitoring and streamlining machine data to providing you with remote diagnostics no matter where you are.
With connectivity and other fleet management software and tools, we can help set you up for success, avoid downtime, predict issues before they arise, and tackle whatever the jobsite throws at you.
What can John Deere's connectivity systems do for your operation?
Reporting, monitoring, and controlling machine operations through connectivity is revolutionizing heavy machinery-based industries. Our systems integrate advanced communication technologies — such as CAN, cellular, satellite, and GPS — into a sophisticated network that meets your needs.
These advanced yet rugged communication products and services give you efficient logistics, reduced maintenance, data management, and cost control — all while withstanding harsh work environments, vibration, and more.
Applications include:
- Track and Trace: These core functions involve using a wireless communications gateway on a piece of equipment with little or no interaction with that equipment. Simple, hard-wired inputs can be made available to collect additional information and report it as required. This can enable things such as location and usage tracking as well as fleet driver management.
- Machine Monitoring: Building on those core functions, the addition of machine monitoring capabilities includes receiving information from an on-board data bus (typically CAN) and enabling access to significant machine information, including alerts, machine performance, and diagnostic trouble codes.
- Productivity and Control: Requiring integration with other components on the machine, this enables information to be received and sent to a machine and/or its operator. This sophisticated interaction makes it possible for machines to receive and react to incoming information, including machine guidance and control, remote diagnostic and repair sessions, and automated jobsite coordination.
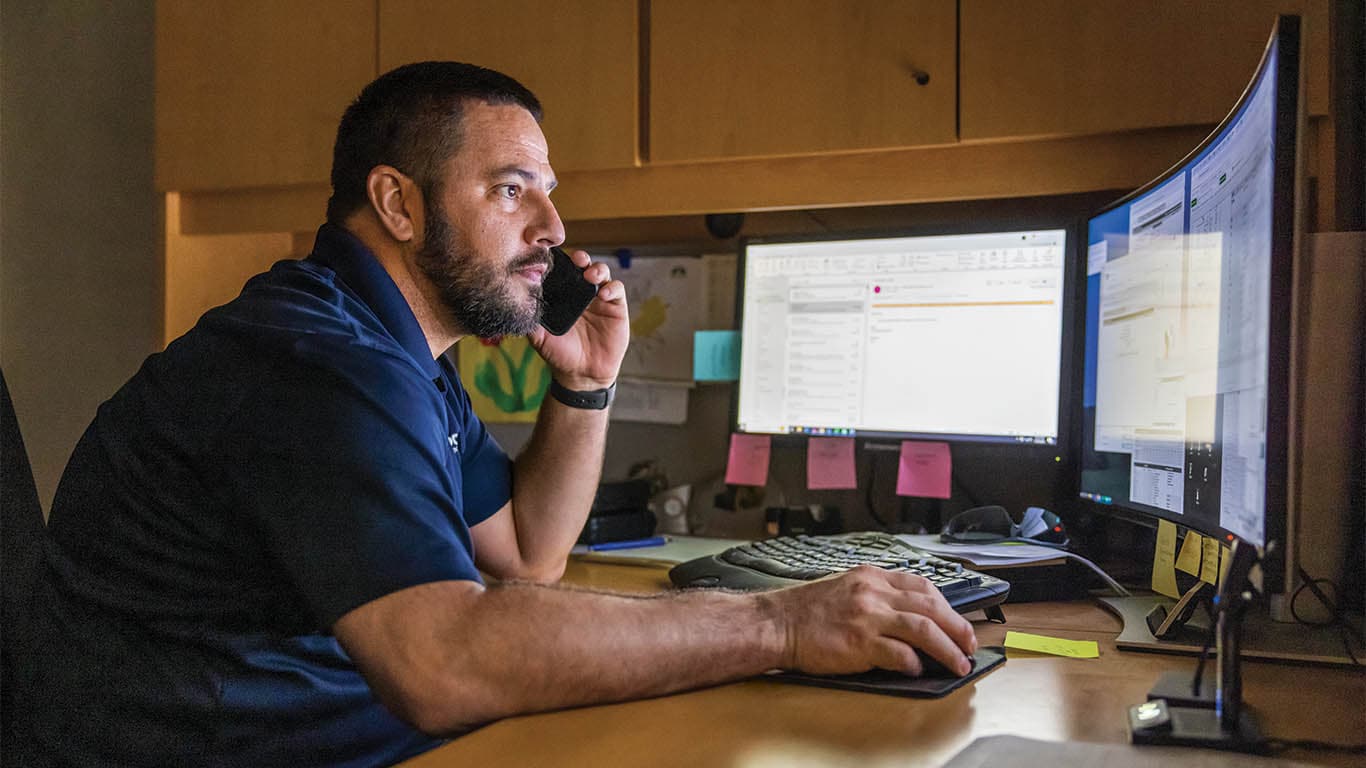
What can the John Deere Operations Center™ add to my business?
Being successful means being efficient — and staying on top of machine performance can make that happen. The John Deere Operations Center can provide you with the heavy equipment monitoring system you need so you can focus on your work.
Specifically designed to help you monitor your machines, the John Deere Operations Center helps you keep a close eye on every detail and gives you more control of your fleet. It's like having construction management software to help you work smarter and tackle issues head-on — before they have a chance to slow you down.
Through the John Deere Operations Center, you can monitor and analyze machine data, track utilization and productivity, find details about machine health information, and more. And with remote diagnostics and our industry-exclusive Expert Alerts system, your dealer can keep eyes on your fleet and troubleshoot machine issues from a distance — sometimes even solving them without a site visit.
John Deere construction equipment is also available with in-base connectivity to help you analyze critical machine data, track utilization, review diagnostic alerts, and more — all from the John Deere Operations Center. Together, this means reduced downtime and elevated efficiency — a win-win.
What is JDLink technology, and how can it help with fleet management?
Standard on most new models, JDLink connectivity provides valuable fleet insights and enables other Precision Construction solutions, making it easy for you to connect machines — and stay connected.
JDLink is the connection that enables automatic data flow between connected machines and the owner's John Deere Operations Center account. JDLink connectivity includes machine data sharing at no additional cost without additional subscriptions or renewals.
With just a few clicks in the Operations Center, the one-time setup activates the service on your current and future JDLink-equipped machines.
The Operations Center can also help you:
- Track machines to make sure they're operating at peak productivity.
- Monitor your fleet nearly in real time.
- Keep tabs on equipment location, time, fuel consumption, engine hours, and engine load levels.
- Connect your machines for fast data transfers and bring connectivity to your entire fleet, regardless of equipment brand or age.
- Keep up to date on your machine and fleet health maintenance information.
- Stream machine and field data to your John Deere Operations Center account.
- Remotely access displays for training and troubleshooting.
From connecting your equipment and data with your team and advisors to monitoring the health and productivity of your fleet, the Operations Center keeps you in constant control no matter where you are.
It also provides you with a direct link to your local dealer. With your permission, your dealer can remotely monitor diagnostic codes and provide proactive equipment service and expert support. That keeps you up and running when it counts most.
Want to learn more?
When you choose a John Deere machine with JDLink and other connectivity solutions, you can lean on construction management software to help you manage your fleet so you can focus your time and efforts on the jobsite.
Ready to learn more about connectivity and how it can provide you with better fleet management? Contact your local John Deere dealer for more details today.
Related Articles
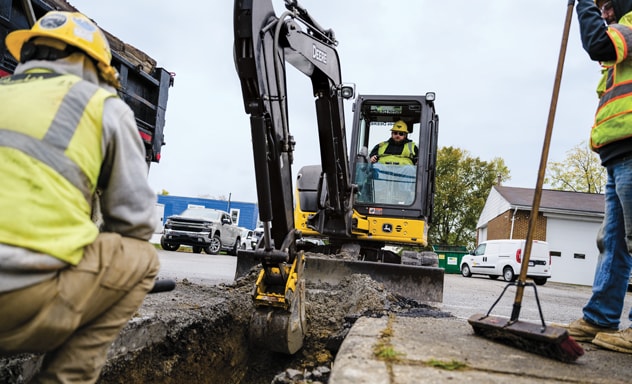
Never Say Never
Aiming High in the West Virginia Underground
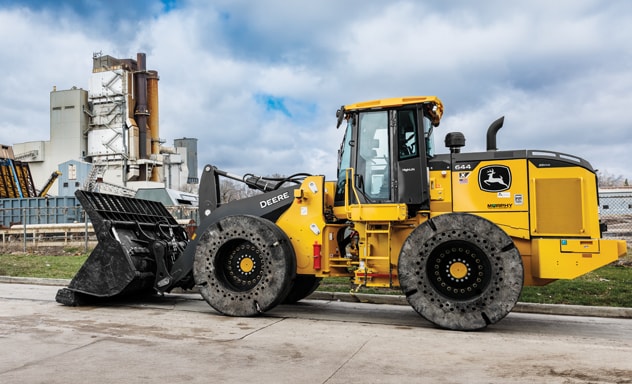
Fuel Sustainability
Iowa Plant Turns Waste into Power