Agriculture, Livestock/Poultry March 01, 2025
Start to Finish
Farmcrest Foods finds success through vertical integration.
by Lorne McClinton
Lots of people say it's impossible to start farming from next to nothing in Canada but Richard Bell begs to differ. As far as he's concerned, Canada has been the land of opportunity. He moved to Canada in 1993 from Northern Ireland with just $200 in his pocket and a passion for poultry. Thirty-one years later his broiler chicken farm and processing facility, Farmcrest Foods Inc., in Salmon Arm, BC, is a marvel. It's Western Canada's only fully vertically integrated chicken operation. If you've ever taken a cruise to Alaska, you've likely eaten his chicken. It's quite the story.
Above. Today Farmcrest Foods is a fully vertically integrated broiler farm. They grow a substantial portion of their own feed and render their processing plant waste onsite into protein meal and fat. The amount of technology and automation in Bell's poultry operation is astounding.
Bicycle job search. "A college friend met me at the Vancouver airport and took me to his family's place in Fraser Valley [BC]," Bell says. "I borrowed a bicycle and started cycling through the valley. If I saw a poultry farm that looked like it would be nice to work at, I'd call in and tell the farmer I'm looking for work. I came across a broiler breeder farm where I thought I'd like to get a job. I gave him the phone number of the place where I was staying and by the time I got home, he'd called and asked me to come back for an interview. He offered me minimum wage, $6.50 an hour, which was the minimum wage at the time. I told him, 'okay I'll start at that, but if I've proven myself in say four months, I want $15.'" He got his raise.
The Fraser Valley is the most concentrated poultry-producing area in North America. There are layers, breeders, broilers, ducks, silkies, turkeys, every type of bird imaginable within just a few miles. Bell thought the concentration made the region a biosecurity timebomb waiting to happen. So, in 1999 he started looking for a farm of his own in the BC Interior. He found one in Salmon Arm that was just what he was looking for. The small breeder broiler operation had eight barns, enough for a full production cycle, and a small, licensed slaughter plant. Having a license already in place was important. It saved Bell from having to jump through all the regulatory hoops that are needed to get one.
"We converted the barns to broilers and started processing about 5,000 birds a week," Bell says. "We upgraded the plant and pushed production. Now we hatch, grow, and feed them. Then we bring them into our processing plant to slaughter, package, and ship them to our customers."
They now have 16 barns. At their peak, prior to Covid when all the restaurants shut down, they were processing up to 80,000 GMO-free birds a week for the fresh and wholesale food services market. They are slowly building their markets up again.
Vertical integration has been a key part of Bell's philosophy right from the start. He's a firm believer in bringing as much of his supply chain into his operation as possible. That's why he built a fully-automated feed mill to make all their pelleted feed, and set up a trucking and logistics company to handle their shipping and receiving internally.
The farm also has 600 acres of Class one river delta land. It allows them to grow a substantial portion of their own feed and lets them capture more value from their manure.
"We've been big on the sustainability since our foundation 25 years ago," Bell says. "We have a lot of chicken manure, so we don't use any chemical fertilizer, our farm has all the chicken manure we need to grow corn, soya, wheat, grass, or whatever."
There's no other poultry operation in Western Canada quite like Bell's. It's the only one that has a rendering plant attached to it. Every chicken plant produces about 70% chicken and 30% waste. While most haul their waste away to dispose of it, Bell's plant renders theirs into protein meal and liquid fat. These are used to fortify their premium Harbell's line of dog food.
"I've been in Canada now for over 30 years, there's not a week goes by that I don't have to pinch myself," Bell says. "There's opportunity everywhere. You just have to be prepared to take risks."
Building a business isn't easy; and capital is always a challenge, Bell says. There's always new technology to invest in. But if you can control your costs and have the right family story to portray, the consumer will pay for it.
But having a good idea is not enough. You need a good bank too, Bell says. You can have all the ideas and opportunities in the world, but if somebody isn't willing to capitalize it, you're dead in the water. It helps a lot if you have a track record, too.
"The first three to five years are the toughest," Bell says. Then, after you've proven yourself to them time and again the bank will start believing in you.
While they took lots of risks, they had a plan and were determined to execute it at all costs. If this meant working 16-hour days, 7-days a week, they did.
"We tried to manage our costs and combine good farm practices with modern facilities," Bell says. "This combined with our never-say-die attitude allowed us to build the highly efficient system we needed to survive. We were also very fortunate that things lined up for us, so we were able to prove ourselves to the bank." ‡
Read More
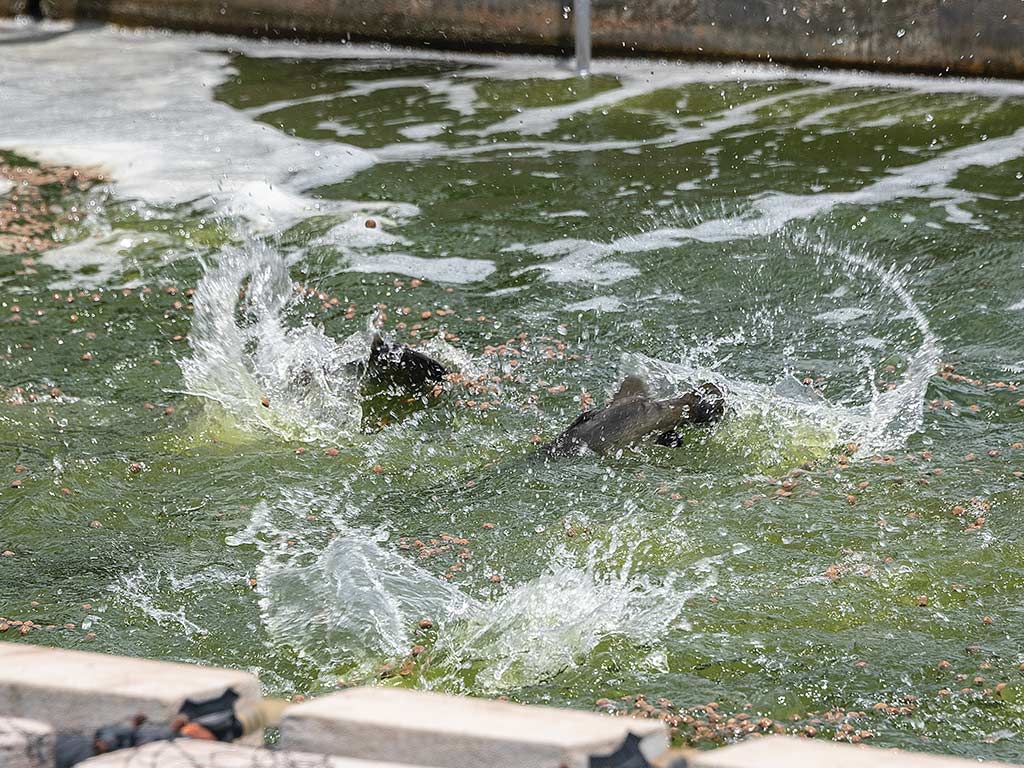
AGRICULTURE, EDUCATION
Fishing for New Markets
US Soybean Export Council builds aquaculture markets.

AGRICULTURE, SPECIALTY/NICHE
Tray-grown Strawberries
Quebec strawberry producer pioneers new method.