Dean Logging
Winter 2025
Overcoming Steep Odds
Dean Logging is winning the uphill battle of steep-slope logging in Oregon
6 MIN READ
Atop a ridge along a logging site about a 90-minute drive south of Eugene, Oregon, Keith Gunn, part-owner of Dean Logging, surveys the scene. The landscape is breathtaking. Green, undulating valleys carve their way through rugged mountains covered in majestic Douglas fir.
The beautiful surroundings belie the challenges of logging this difficult terrain. In the past, the wood was hand-felled before being extracted by yarders with the help of choker setters and spotters.
Across the valley, Gunn watches a lone John Deere 959ML Shovel Logger maneuvering along a steep incline, moving logs within reach of the yarder. Up above a yarder operator retrieves logs with a grapple car mounted with a camera, which allows him to grab logs without the need for a spotter.
"It's all mechanized logging on this side," Gunn explains. "Before we had fi ve or six workers on the ground. Now we have zero. It's a lot more efficient."
The company also tethers a John Deere Tracked 959M Feller Buncher and a Deere 768L-II Bogie Skidder. The approach has helped reduce, although not eliminate, boots on the ground.
TALL ORDER
Over half, or 30 million acres, of Oregon's landmass is covered by forest. The sheer size of the timber leaves little doubt as to why Oregon produces more softwood lumber and timber than any other U.S. state. That is until one considers the terrain. Not a lot of flat area. It's mostly vertical. "It's all steep slope logging here," observes Gunn.
Skyline yarding is the most common type of operation in Oregon. Before becoming part owner, Gunn "tended hook," which meant overseeing a yarder crew, or "side" as he calls it.
"There's a lot to learn about tending hook," he says. "It's more than just moving the yarder and stringing wire through the woods. Managing people and making sure everyone is doing what needs to be done is key. And there are tricks and different things you can do to make everything more productive."
Mechanization is one of those tricks. In the two years since becoming part owner, Gunn has started running numerous tethered machines, including the 959ML Shovel Logger and a six-wheel 768L-II Bogie Skidder for shoveling as well as a 959M Tracked Feller Buncher. "We never did any of our own cutting before becoming more mechanized," says Gunn. "The bogie skidder also runs mostly on tether because it's great on steep slopes."
Each side typically averages 12 to 14 loads per day. Mechanization has made felling and extracting wood more efficient. The terrain often creates challenges for managing the wood when it reaches the landing. Typically, the processor will grab logs out of the shoot and process them. The shovel will then deck them or load them onto a truck. In tight areas, operators need to be more flexible. Conditions might make it necessary to use the processor for both processing and loading.
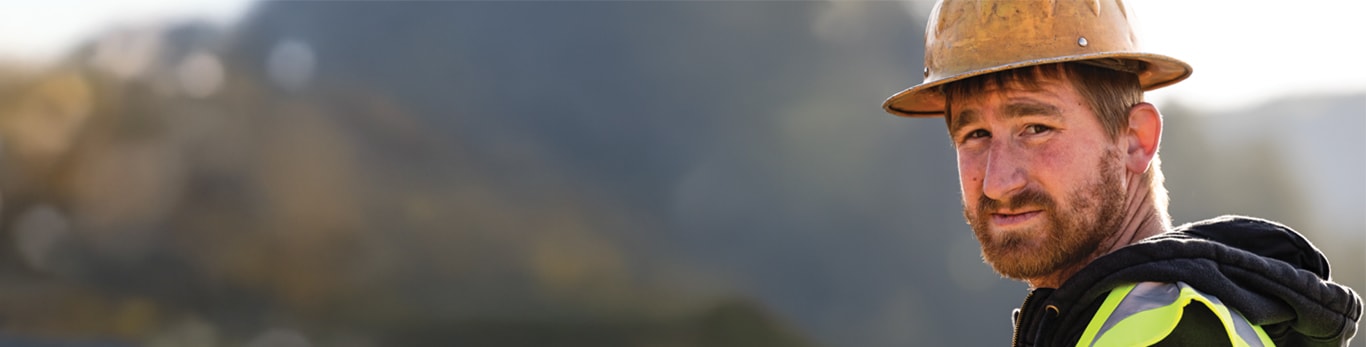
"Before we had five or six workers on the ground. Now we have zero. It's a lot more efficient."
STEEP LEARNING CURVE
Gunn's grandfather, Ray Dean, started the company in 1973. Unlike many who are raised in logging families, Gunn didn't grow up around logging. "I didn't do any work in the woods until I graduated from high school in 2010. I'd worked in a gas station and a truck stop. I didn't want to go to school, and I wanted to make something of myself. Logging seemed like the best opportunity."
As Thomas Edison observed, most people miss opportunity because it is dressed in overalls and looks like work. Kitted out in work clothes, a hard hat, steel-toed boots, and other personal protective equipment (PPE), Gunn headed off into the woods in search of his future. And to set chokers.
Choker setting is physical, exhausting work. "It's pretty tough," says Gunn. "When you start out you're like a baby deer, flopping around and falling over everything. But then you learn how to walk properly in the woods, raising your legs so you don't fall down and use less energy. You actually start to count your steps, so you might be taking 12 easier steps across a hill instead of 10 more difficult steps up."
To be a decent logger, Gunn believes you must start at the bottom and work your way up. "You can't start in the middle, but it's not what most young people want to do today."
After several years as a choker setter, Gunn worked his way up, spending several years running yarders, processors, and shovels to learn how the whole operation worked. He then tended hook for five years before becoming a part owner.
CONTINUING A LEGACY
Dean Logging bought its first John Deere machine in 2012. "Since then, it's been all Deere," says Gunn. "Our 3156G Swing Machine is great. It's big and can handle anything we throw at it. We use it mainly for loading."
A big reason Dean Logging runs Deere is the common filters and fluids, which make them easy to maintain.
Uptime is crucial to keeping everything rolling. "Our local dealer, Papé Machinery, does a great job taking care of us," says Gunn. "If we ever have a problem, they jump right in. Parts are usually available the same or next day."
Good equipment and support are important, but ultimately Gunn owes the company's success to its employees. Many have been with the company from five to fifteen years. "We have great people who really care about doing the right things and being safe," says Gunn. "We all have the same goals and really feel that we're part of something."
"Dean Logging has always had an exemplary reputation," observes Greg Staten, territory manager, equipment sales, Papé Machinery. "They do quality work and are well-liked in the community. They have been in business over 30 years and, with Keith at the helm, probably 30 or 40 more. It's neat to see the legacy of a successful business passing through generations."
"I'm proud to carry on a well-established business," adds Gunn. "I just want to continue to make a good name for Dean Logging and my family."
Dean Logging is serviced by Papé Machinery, Central Point, Oregon
Related Articles
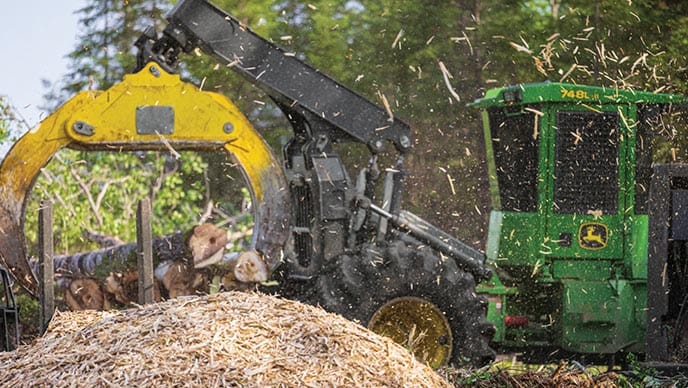
When the Chips Are Down
The people at Carlson Timber Products are there for each other, even in the toughest times.
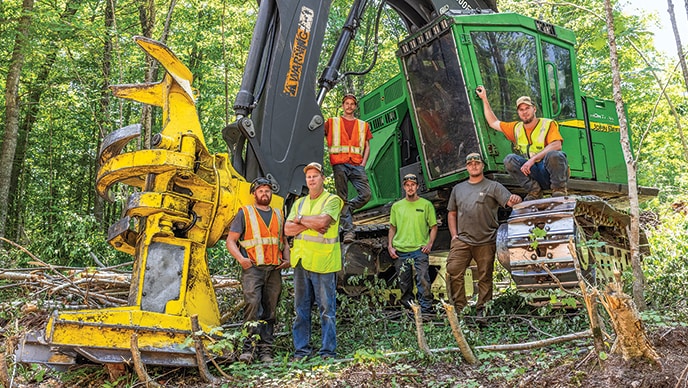
Front Man
A multigenerational logging company finds success by embracing teamwork and new technology.
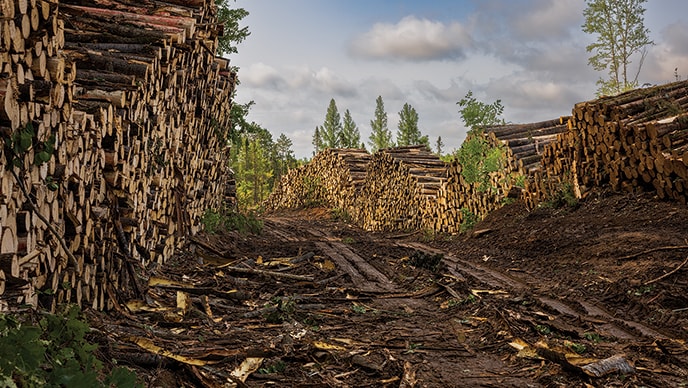
The Marshall Plan
Marshall Logging continues eight decades of logging by adapting to change and adopting new technology.
Do you think your company's story would resonate with others in the logging industry?
SHARE YOUR JOURNEY