UTILIZING RECYCLED ASPHALT FOR SUSTAINABLE, COST-EFFECTIVE ROADBUILDING
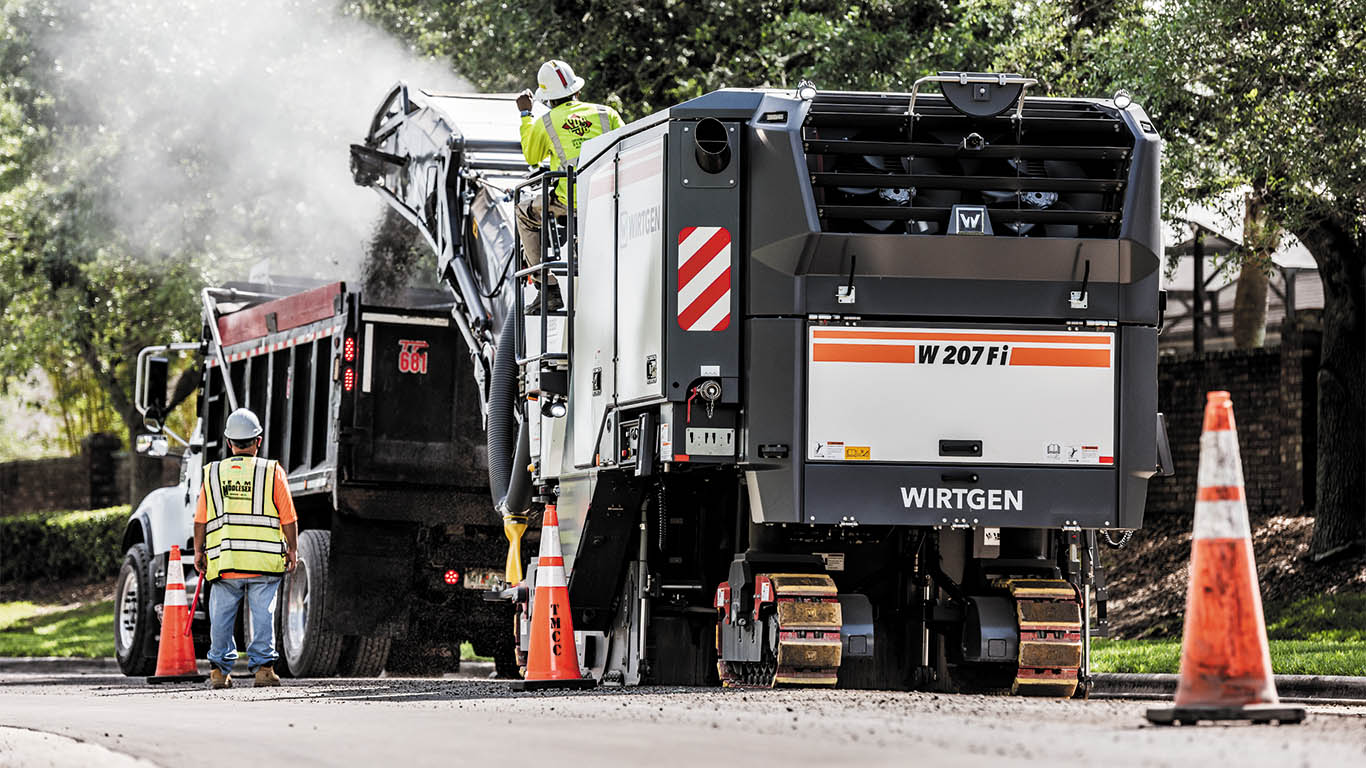
When you think about recycling and conservation, things like plastic bottles, aluminum cans, cardboard boxes, and reusable alternatives probably come to mind. But if you work in the roadbuilding or aggregate sectors, you should also be thinking about asphalt.
In industrially developed countries, significantly more roads are rehabilitated or extended than entirely new ones are built. According to the National Asphalt Pavement Association (NAPA), more than 94 million tons of reclaimed asphalt pavement (RAP) was recycled into new mixes in 2021 — an 8.74% increase from 2020.
From a conservation standpoint, there are many reasons why you should recycle asphalt and utilize recycled asphalt — from cost and resource savings to reducing your carbon footprint — but it has several other advantages, too. Not only is it cost effective and sustainable, it's also quite durable. In laboratory and field evaluations on mixtures containing high levels of RAP, researchers have indicated that the structural performance of recycled mixes is equal to — and in some instances, better than — that of conventional mixes, according to NAPA.
Here is a brief overview of asphalt recycling and how John Deere and The Wirtgen Group can help you reduce, reuse, and repave when it comes to sustainable road construction.
Better for the planet — and your bottom line.
There are many economic and environmental benefits of asphalt recycling for roadbuilding projects, especially when it comes to conserving natural resources. Not only can RAP be used for any number of applications, but using the maximum amount of it also positively affects RAP prices.
RAP is a completely recyclable material that can be used over and again, which reduces the need for costly new materials, according to NAPA. The organization says that using RAP saves some $3.3 billion annually. Nationally, the average 21.1% RAP that's used in new asphalt mixtures saves $7.80 per ton compared to mixtures that contain all virgin materials, according to NAPA.
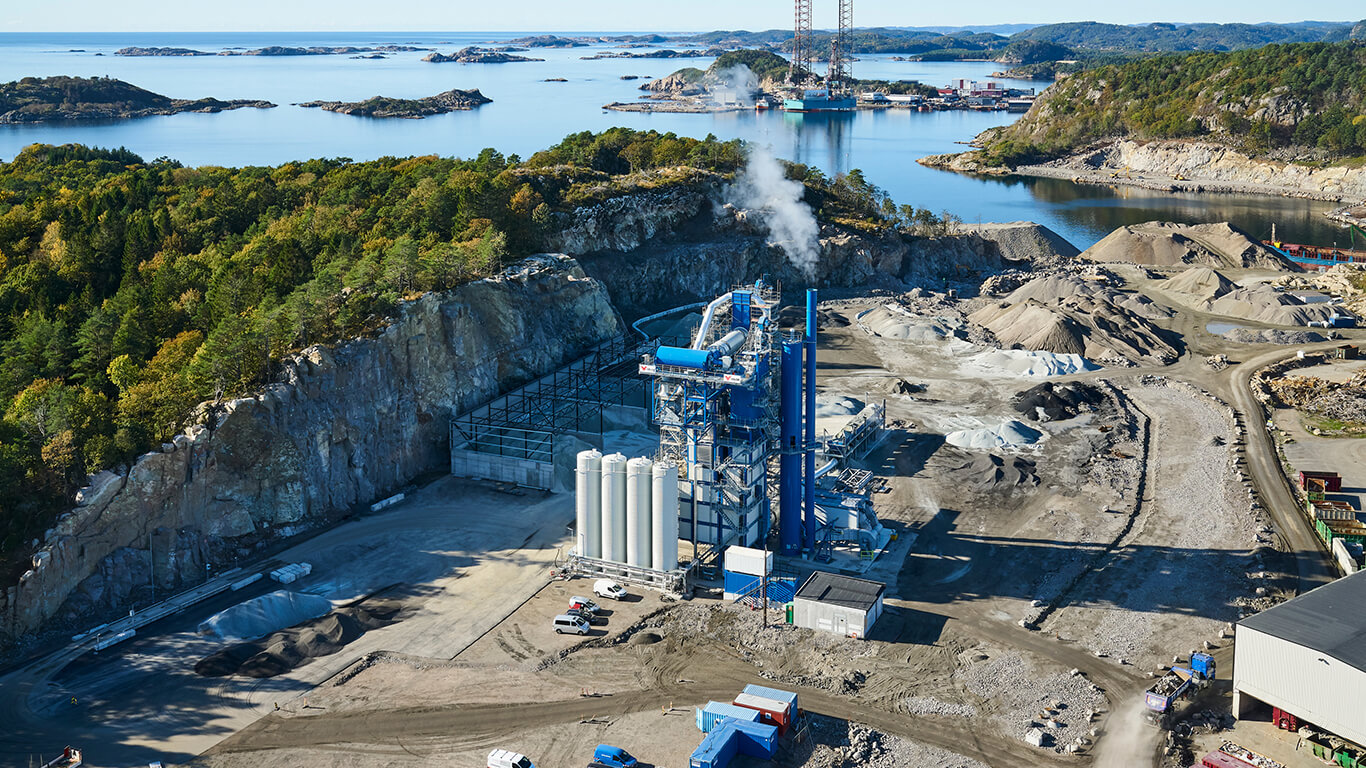
Limit what you emit while conserving materials.
A member of the John Deere family, the Wirtgen Group and its six premium brands — including Wirtgen, Vögele, Hamm, Kleemann, Benninghoven, and Ciber — serve the road construction, quarry, and aggregate sectors. Benninghoven in particular offers recycling technologies — including hot or cold feeder systems – for every customer need.
Benninghoven's leading, patented recycling technology allows plant owners to produce an asphaltic mixture from 100% reclaimed asphalt while meeting stringent air quality control limits. Take for example Benninghoven's counterflow recycling drum with a hot gas generator. Direct firing throughout the recycling process tends to "burn" recycled materials coated with bitumen, or at least impair its properties. The hot gas generator, however, indirectly heats the material, gently raising the temperature for optimum processing.
Cold recyclers may also be used to prepare asphalt pavement on site to help conserve materials. During this process, existing pavement is granulated with the milling and mixing rotor and prepared by adding precise amounts of bituminous binding agents, cement, and water. This results in a homogeneous material that can be used to directly repave the soil.
Whether you produce it or simply use it, choosing RAP over all-new materials helps cut down on emissions. According to NAPA, the net reduction of greenhouse gas emissions from the use of RAP in new asphalt mixtures from 2009 to 2019 was estimated at 21.2 million tonne CO2e — which is equal to the annual emissions from about 460,000 passenger vehicles.
Beyond reducing emissions, recycling asphalt also lessens the need for additional materials. Because the materials are gently and indirectly heated in counterflow processing such as Benninghoven's, any bitumen contained in the material is not combusted and may continue to serve as a binding agent. In 2022, RAP usage reduced the need for roughly 26.9 million barrels of asphalt binder and more than 93 million tons of aggregate, according to NAPA.
And because more materials are used throughout the asphalt recycling processes, fewer materials are thrown away. NAPA reported that RAP stored for future use in 2022 also saved some 68.2 million cubic yards of landfill space.
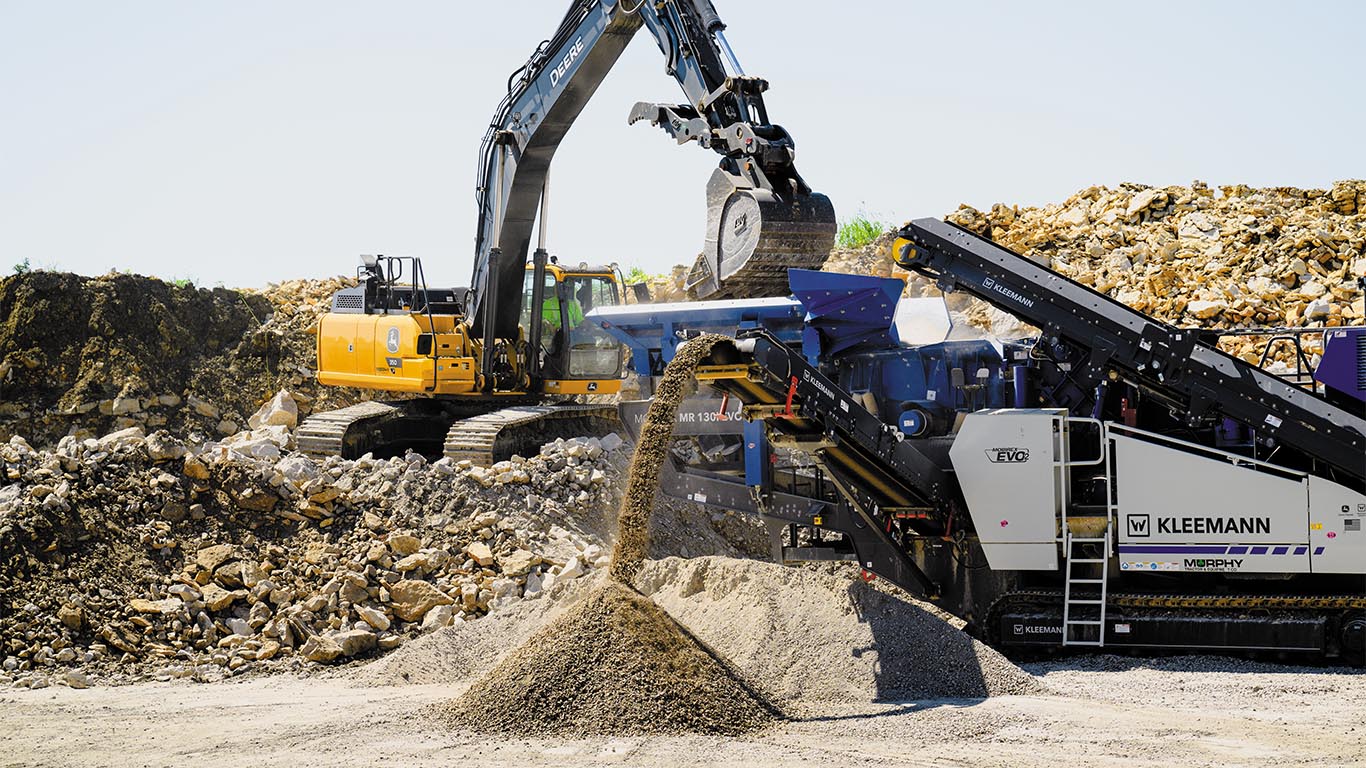
How can John Deere and the Wirtgen Group help?
John Deere and the Wirtgen Group are leaders in roadbuilding solutions, offering a wide range of equipment to help you complete any roadbuilding task and beyond — from excavators, backhoes, wheel loaders, compact track loaders, skid steers, dozers, motor graders, and articulated dump trucks (ADTs), to pavers, crushers, screeners, milling machines, and much more.
From applying recycled asphalt to brand-new roads, resurfaced neighborhood streets, and everything in between, we can help you choose the right equipment for the job so you can focus on getting it done.
We also offer highly trained technicians and specialists, parts whenever and wherever you need them, and more. Our expansive, world-class dealer network helps keep your equipment up and running while helping you decrease costs, work toward your sustainability goals, and stay on top of your operations.
Ready to learn more about adding John Deere and the Wirtgen Group roadbuilding equipment to your fleet? Contact your local John Deere dealer or the Wirtgen Group dealer today.