John Deere and Ford Team Up to Create a Concept Gator Made of Recycled Parts
Concept vehicle helps Deere explore how to use sustainable materials in its machines
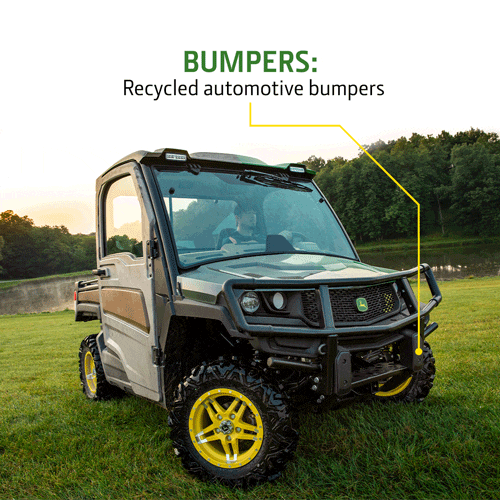
When you picture a collaboration between Ford and John Deere, what comes to mind?
Horsepower? Diesel?
A hood made of plastic bottles pulled from the Mississippi River or a storage bin made of coconut filler probably wasn’t your first thought.
These are just two of the many surprising materials used to produce a new Sustainable Concept Gator, a one-of-a-kind machine prototype built in collaboration with Ford Motor Company’s Sustainable Materials team to examine ways of taking waste streams, like plastic bottles, and turning them into viable machine components.
“When the idea of the Sustainable Concept Gator project came about, the goal was to explore a variety of materials to be used for possible adoption across product lines to support our goals around increasing use of sustainable materials,” Andy Greenlee, senior staff engineer for sustainable solutions at John Deere, said.
Collaborating with industry experts
Working with Ford on the project was a perfect fit, Greenlee said.
“Ford is a long-time leader in sustainable materials and has been integrating sustainable parts into their vehicles for decades – even back to Henry Ford experimenting with soybean oil in the 1930s,” he said.
Getting the opportunity to look at things that are out in the future and focus on what we need to develop to add value to our customers while reducing our environmental footprint was a great experience.
Greenlee was one of six Deere employees on the team tasked with developing the Sustainable Concept Gator. While the project presented many challenges, the team worked closely with both Deere and Ford’s network of suppliers, many going above and beyond to support the project, to build a prototype created with renewable, recycled, and recyclable materials such as soybeans, flax fiber, sugar cane, hemp fiber, bottles, and even fishing nets.
“It was difficult because we had to work within our current framework of production tooling, we weren’t going to invest in new tooling for a product that won’t go to market, but we did everything we could to find sustainable materials that were suitable replacements,” Keith Shanter, senior materials engineer, said.
Why build a vehicle that will never go to market?
Concept projects like the Sustainable Concept Gator are extremely valuable to our efforts in sustainable innovation, Jill Sanchez, director of sustainability, said.
“The Sustainable Concept Gator has provided us key learnings,” Sanchez said. “It shows how innovative thinking and innovative partnerships provide invaluable insight into how we can apply sustainable material use in the future.”
Though many components used in the Sustainable Concept Gator are not a short-term production solution, the materials pave the way for sustainable solutions, including one that is in production now.
“One component from this project that’s in Gators produced today is a defrost louver made out of recycled tires,” Shanter said.
When reflecting on the project, which started back in 2018, both Shanter and Greenlee appreciated the opportunity to not only learn from the experts at Ford but found it inspiring to work on a future-focused project that has the potential to make a big difference.
“Getting the opportunity to look at things that are out in the future and focus on what we need to develop to add value to our customers while reducing our environmental footprint was a great experience,” Greenlee said.